On March 13, 2023, a momentous occasion in the history of mining development in Mongolia was marked by the commencement ceremony of the Oyutolgoi underground production. The event was attended by the Prime Minister of Mongolia L.Oyun-Erdene, and the CEO of Rio Tinto Group Jakob Stausholm, who jointly announced the commencement of underground production by tightening the screws of the plaque. “The Oyutolgoi underground mine has the potential to produce 500,000 tonnes of copper concentrate annually, and to elevate the GDP per capita to USD 10,000, thereby making this long-time goal a reality,” addressed the Prime Minister. Rio Tinto’s CEO Jakob stated “Over the past six years, thousands of Mongolian youth and local experts have worked tirelessly to construct this underground mine. The miners working underground are supported by thousands of employees from the Gobi region, Ulaanbaatar in Mongolia, Brisbane in Australia, and from all corners of the globe. The workers of Oyutolgoi gathered in a specially prepared hall to mark the commencement of underground production. During the ceremony, several workers shared their impressions of this historic event.
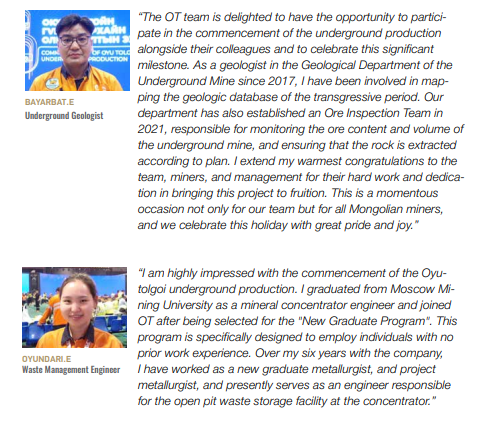
OT is committed to contributing to Mongolia's economy and enhancing its ability to compete on the global stage by fully developing underground and open-pit mines. This historic project, which began over 60 years ago with a group of more than 60 explorers, has evolved into a stateof-the-art operation that utilizes advanced technical and technological solutions to produce over 1,265 metric tonnes of ore per hour. The company is dedicated to sustainable operations and is proud to share its innovative approach to mining with the world.
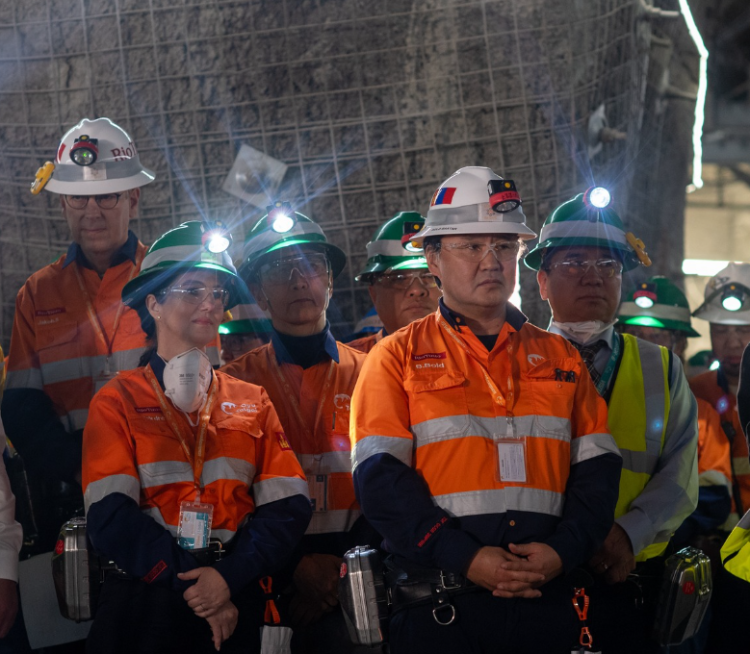
Given that underground mining is a 24-hour continuous operation, safety is of utmost importance to underground miners. A workforce of 700-800 individuals operates during the day shift, while 500- 600 individuals work during the evening shift, ensuring that the highest standards of safety and construction are upheld around the clock. The team embarked on their journey at the bottom of the three-block mining levels of the underground mine, where ore falls under its weight after blasting, making it a pickup point. This location is situated beneath a massive ore body containing the highest grade of the OT deposit, which will be extracted through block demolition from below. The block-caving mining method has the advantage of reducing production costs in the long run, but initial costs can be high.
Additionally, underground mining has less environmental impact than openpit mining, as only the necessary ore is extracted through the block and demolition method, unlike in open-pit mines where 3-5 tonnes of soil must be removed to extract a ton of ore. This state-of-the-art technology is being introduced to Mongolia for the first time. Underground Chief Training Officer N.Erhembayar explains, “Safety is a top priority for workers in the mine. Concrete supports are installed in every tunnel of the mine to prevent small stones from falling on workers. The concrete used is quickdrying and reinforced with capillary fibers. When the mine is blasted, two-meter-long cracks are formed, which are fixed by drilling 2.4-meter-long reinforcing bolts with glue in addition to the concrete supports. Each bolt undergoes a pull test with a force of 15 tonnes.” Also, geotechnical engineers conduct monthly inspections of the fractures, and miners are responsible for reporting any rock noises they hear. Over 350 vehicles and mobile equipment are used in the underground mine. Due to the continuous operation of these machines and mechanisms for 24 hours, air conditioning is necessary to regulate the heat generated. The Administration and Service Center on the surface will monitor the number of people and equipment working in the underground mine, and regulate the air accordingly to ensure a safe and comfortable working environment. As journalists, we proceeded to the next stage where the crusher is located, and loaders dump the ore into the tunnel visible in the background. The ore is then transported from the mining site to the primary crusher.
At full capacity, the crusher can crush 95,000 tonnes of ore per day, which means the underground mine can be used for 108 years. Concrete arches and pillars are used to support the tunnels leading to the crusher to ensure the safety of the workers. After the primary crusher, the ore is transported to the concentrator via an 8.2 km long conveyor belt. The ore extracted from underground is combined with the open pit ore and transported via a conveyor to the concentrator. At present, most of the open pit ore is processed at the concentrator, however, with the stabilization of underground production, 90% of the concentrator's processing capacity will be used for the underground ore. Using the flotation method, the plant produces a concentrate with a copper content of approximately 21%. Operations Manager of the Concentration Plant D.Budragchaa explains that by processing ore with a high concentration of copper from the underground mine, the overall copper content of the concentrate will increase, resulting in the production of 1-3 times more final products. Water consumption is one of the special concerns in the OT project. Although the production volume and concentrate output from the underground mines are expected to increase, the concentrator's mill throughput will remain the same to minimize water consumption.
The mill will continue to process 100,000-120,000 tonnes of ore per day, which requires over 60,000 tonnes of water. The average water reuse rate is 88 percent depending on the season.
Once produced, the copper concentrate from the concentrator will be stored in an open warehouse before being packaged into two-tonne bags, which are then sealed for export. The concentrating and packaging plants will need to be expanded to accommodate the increased production from the underground mine. At the end of the tour, the journalists paid tribute to the statue of D.Garamjav (1945-2018), a highly esteemed geologist in Mongolia. Garamjav devoted much of his career to the study of copper mineralization at OT, beginning in 1983. Due to his significant contributions to the mining industry, he is commonly referred to as "Copper Garamjav". A Mongolian flag flies opposite the statue of the honored geologist, symbolizing the cooperation of many domestic and foreign experts who have devoted their efforts and knowledge to the construction of OT. The flags of 25 countries, including Australia, South Africa, New Zealand, Norway, Russia, Singapore, Indonesia, Hungary, Finland, the Philippines, France, Turkey, Canada, Bolivia, the United States, China, Pakistan, Spain, the Netherlands, Georgia, Mexico, Brazil, and Niger, stand side by side, representing the international scale of the Oyutolgoi copper-gold mine. The path to OT’s development has not been without its challenges. Since the investment agreement was signed, the project has been implemented amidst social controversies and debates over its profitability for Mongolia.
Between the first quarter of 2010 and 2022, OT spent a total of USD 13.8 billion, with 74 percent, or USD 10.2 billion, of purchases made with national companies. If planning for the underground mine started in 2005, it has taken 18 years for mining to finally begin. The underground mine is an enormous four-layered structure with 120 km of roads inside. Although construction is not yet complete, it will continue. It will be a long journey ahead.
Mining Insight Magazine №3 (016), March 2023