Mining Insight's Ariuntuya. N and Bold-Erdene. S interviewed with Yondon. G, General Director of Erdenet Mining Corporation SOE.
In your address delivered during Mining Week 2023, you highlighted the deteriorating geological conditions at the Erdenet mine, along with rising costs due to declining ore grade. It was suggested that the establishment of a copper concentrate smelter could address numerous challenges confronting the Erdenet Mining Corporation (EMC). Could you please elaborate on this reasoning for our readers?
2023 holds immense significance for Erdenet, marking the 60th anniversary of the discovery of the Erdenet Ovoo deposit by geologists from Mongolia and the Czech Republic. It also commemorates the 50th anniversary of the establishment of the agreement between the Government of the Republic of Korea and the Soviet Union for the joint use of the deposit (in its former name), and the 45th anniversary of the commissioning of the EMC with a production capacity of 4 million tonnes, culminating in the production of the initial concentrate. Over time, geological conditions tend to deteriorate at most mines. Simultaneously, mines tend to exploit their most profitable sections to swiftly recover their investments. As mines extend deeper, metal content diminishes, and ore hardness increases. This trend is also observable at the EMC, now in its 45th year of operation. The copper content in the ore, a fundamental geological parameter, exhibits an annual decline, leading to a reduction in marketable product quantities. One of the proactive measures taken to counter this challenge is the expansion of ore mining and beneficiation capacity. Last year, we augmented our ore beneficiation project capacity by 6 million tonnes, reaching a total of 38 million tonnes. Currently, efforts are underway to further increase this capacity by an additional 2 million tonnes. In 1978, the plant processed 4 million tonnes of ore.
By 2024, the capacity will have expanded to 38 million tonnes, and it is projected to reach 40 million tonnes by 2025, akin to Oyu Tolgoi. However, it's worth noting that the metal content in Oyu Tolgoi ore is on the rise, with the operation of the high-grade Hugo Dummet section commencing in 2022. This will result in a nearly threefold increase in ore content entering the factory starting in 2028. In stark contrast, the grade of Erdenet ore is consistently diminishing and is forecasted to be 0.38% in 2024, a notable decline from 0.416% in 2023.
As the ore grade declines, the copper content in the produced concentrate also decreases. Initially, Erdenet's concentrate boasted a copper content of over 30%, but today, it stands at 22.5%. This reduction in copper content signifies a decrease in quality, posing a potential risk in sales. Under our contracts with buyers, falling below the specified content results in penalties, while exceeding it entails bonuses. As the ore grade diminishes, the recovery of metal from the concentrator's ore decreases. Although ore processing capacity is on the rise, concentrate production needs to catch up, failing to counterbalance the declining grade. While we have planned to process 38 million tonnes of ore in 2024, an increase from the current year, the amount of concentrate available for sale has dropped by more than 30 thousand tonnes. This signifies a decrease in our primary selling point, which is concentrated, consequently leading to reduced profits. Furthermore, the ore's hardness is increasing, with the average ore hardness surging by 25% in the last decade. Consequently, electricity consumption for processing 1 tonne of ore has risen by 20%. Additionally, electricity prices have increased by 37% since November 2022. Moreover, the distance for transporting ore from the mine has extended, further elevating costs and worsening our economic situation. In response, in 2024, we focus on costsaving measures in all aspects rather than expanding our workforce. It's crucial to note that the challenges faced at Erdenet are not unique to this mine alone; they are pervasive in mining operations worldwide. Moreover, the average grade of copper in mines globally has decreased by approximately 30% over the past two decades. This trend is anticipated to persist in the years ahead. The reduction in ore content is a geological reality that necessitates addressing, and there is no feasible way to reverse or halt this natural process.
How does the construction of a smelter offer a solution to these challenges?
If the current circumstances persist, the economic condition and profitability of the plant will continue to deteriorate. Our avenue to increase profits lies in the production of value-added products. Given the challenging geological conditions, the most viable strategy to enhance the profitability andcompetitiveness of the plant is to construct a smelter and boost profits from the subsequent production stage. By establishing an SKS technology plant, which offers cost advantages over many other technologies in the copper concentrate smelting and processing industry, we can efficiently melt concentrate with 18% copper content, resulting in the production of cathode copper. In other words, by reducing the copper content in the concentrate to 20% or even 18%, without imposing constraints or complications on the concentration process and technological steps, we can maintain or potentially increase the metal recovery at the current level. This approach would reduce the marginal content of mined ore, ultimately extending the mine's lifespan. From a broader perspective, this approach offers numerous advantages. Our team has conducted economic assessments and calculated the annual increase in copper production.
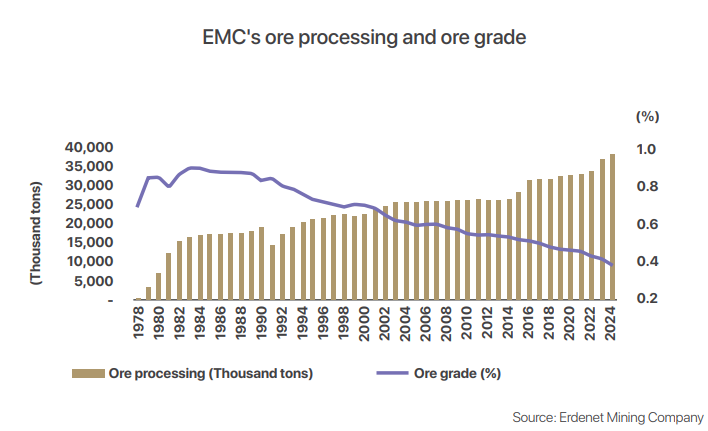
During Mining Week, China ENFI Engineering, the largest state-owned non-ferrous metallurgical design institute in China, which has a long-standing collaboration with our company and was invited by us, presented a plan to increase the concentrate content for use in the copper smelting plant to 14-16%. With the production of such lower-grade concentrates, it's possible to economically mine ore with a grade as low as 0.3% or even 0.2%. Notably, deposits with a 0.2% grade are still being utilized in Canada. Conversely, in recent years, Chinese refineries have been progressively elevating their standards for copper concentrate quality. China's environmental regulations are becoming increasingly stringent, with some standards even surpassing those in Europe. While the copper content in the concentrate must not drop below 22%, there is a growing demand to reduce arsenic and fluorine content. These requirements are becoming increasingly challenging to fulfill as the copper content in our ores and concentrate steadily declines. Constructing your smelter provides the ability to monitor, manage, and regulate the content of entering concentrates, as well as the levels of useful and harmful elements within them. China recently lowered the arsenic content in concentrate from 0.5 to 0.4. The proximity of a smelter has a positive impact on railway throughput and cargo circulation. It reduces the cost of transporting products. The transportation of 600,000 tonnes of concentrate places a significant burden on our country's railways. Establishing a smelter near your facility is estimated to save approximately MNT 40 billion per year in transportation expenses. Conversely, the diminishing copper content in ore and concentrate negatively affects competitiveness.
The EMC processes ore with a grade of 0.38% to produce a concentrate with a grade of 22.5%. In contrast, the Kamoa-Kakula deposit discovered by Robert Friedland in Congo yields ore with a high grade of 5.0-6.0% and produces a concentrate with a copper grade of 50.0%.
South America boasts the world's largest copper reserves, and Africa has now become a formidable competitor to Latin America. Historically, Chile held the top position, with Peru in second place. China's demand for copper is exceptionally high. A significant portion of the copper mined in Latin America is destined for China. In addition to purchasing half of the world's copper concentrate, China has announced plans to buy 3.0 million tonnes of pure copper in 2024, amassing substantial strategic copper reserves as part of its policy. China is also deeply engaged in smelting and refining, with the refined copper being distributed globally after melting. China's influence is significant in the copper market, effectively dominating it. Notably, the London Metal Exchange has already been acquired by Hong Kong. China's total copper concentrate smelting and processing plant capacity stands at 11.4 million tonnes, and future expansion is expected. Internationally announced projects are anticipated to boost copper concentrate smelting and processing capacity to 24.6 million tonnes by 2022 and 35.6 million tonnes by 2027. Plants like the Kamoa-Kakula plant in Congo, the Freeport McMoRan plant in Indonesia, and the Adani smelter in India are currently under construction, highlighting the high profitability of cost-absorbing industries in the next stage.
Copper smelting research in Mongolia has been ongoing for an extended period. Numerous contentious matters have arisen, including the selection of the smelting location, the choice of technology, and methods to address the management of hazardous elements generated during the smelting process. What underlies the decision to adopt SKS technology at the Erdenet smelter, and what are the key advantages it holds over alternative technologies?
Extensive calculations and feasibility studies were conducted at the EMC to determine the most suitable technical and technological approach for a copper concentrate smelting and processing plant. Over the years, various technologies were considered, including the 1987 Russian "Giprocsvetmet" Vanyukov technology, the 1995 Canadian "Noranda Minerals Inc, Canada" BGRIMM Institute Norando technology, the 1997 Australian "Ausmelt Ltd" Ausmelt technology, the 1999 Russian "Giprocsvetmet" PJV technology, the 2002 Finnish OUTOTEC Flash Smelting technology, and the 2022 Chinese ENFI SKS and Double SKS technology. The selection process was based on several critical factors, such as plant capacity, costs, and whether it would be a standalone facility or part of a larger complex. Cost played a significant role in choosing the smelting technology. The cost of copper smelting per tonne is USD 324 in high-capacity factories, USD 476 in medium-capacity factories, and USD 485 in low-capacity factories, with capacities up to 900,000 tonnes considered low.
Therefore, it was advantageous for Erdenet mine's to be designed not only for its current 560 thousand tonnes of concentrate but also to increase its capacity for processing more concentrate. SKS technology stands out with an operating cost of USD 248 per tonne of copper, approximately USD 200 less than other technologies. These studies indicate that SKS technology offers superior economic viability, characterized by lower operating and investment costs. Generally, a standalone smelter tends to have a relatively low internal rate of return (IRR), typically around 6-7% or less than 10%. Therefore, relying solely on cathode copper sales is not economically profitable. Projects with a high content of accompanying gold and silver, like Oyu Tolgoi, achieve higher returns, but Erdenet's gold and silver content is low, resulting in relatively modest profits. The primary source of profit will come from associated industries. Furthermore, environmental considerations have become increasingly important, with Environmental, Social, and Governance (ESG) issues and carbon reduction policies gaining significance. Hence, the choice of smelting technology had to be based not only on economic factors but also on the need to align with environmental concerns. Taking all these factors and requirements into account, SKS technology emerges as the most optimal choice.
How are environmental concerns assessed, and what strategies are employed to manage harmful elements that are no longer usable?
Dealing with sulfuric acid generated during copper smelting has historically presented challenges. Opponents of such projects often argue that the sulfuric acid produced can be harmful. However, it's essential to clarify that copper smelting initially generates sulfur dioxide gas, not sulfuric acid. The key question is whether to convert this gas into sulfuric acid or not. Current processes and standards are primarily focused on detoxifying and neutralizing sulfur dioxide, with the primary objective being to render it harmless to the environment. The smelter aims to profit from the cathode copper it produces but incurs costs in the sulfur dioxide neutralization process. Various by-products from this process, such as phosphorus fertilizers, elemental sulfur, and hydrogen fluoride production, do not serve as profit sources but rather contribute to reducing the cost of neutralization. The potential use of Khuvsgul phosphorite deposits to manufacture phosphorous fertilizers for the Erdenet smelter has been under consideration since the 1980s. However, this approach involves significant expenses related to concentrate production and establishing transportation infrastructure, whether by rail or road. Additionally, the challenge lies in finding suitable markets for phosphorus fertilizers. Given that China is the global leader in phosphorite fertilizer production, and Russia ranks fourth, it becomes apparent that neither of the two neighboring countries is a likely customer. Furthermore, domestic demand is limited. Nevertheless, ongoing research in collaboration with the Academy continues in this direction, maintaining a proactive stance in readiness for the potential of food shortages in the future. There are plans to produce elemental sulfur from sulfur dioxide, with cooperation from technology experts in this field. Working alongside "ENFI engineering," laboratory tests and semi-production trials have been successfully conducted. A pilot plant has been established, currently undergoing production trials set to conclude in November. Another aspect to consider is the production of hydrogen fluoride. On Erdenet's directive, a Swiss company researched utilizing Bor-Undur fluorspar deposits for hydrogen fluoride production. While, at the current level of industrialization in our country, it might result in products with higher costs and lower consumption, from a scientific and research perspective, we maintain an ongoing interest and commitment to exploring this avenue. Addressing the management of harmful elements like arsenic, which are released during the smelting process, is another concern. According to the feasibility study conductedby ENFI at our request, two key points have been established: first, Erdenet's ore has very low arsenic content and second, arsenic is effectively captured through freezing technology by reacting with other minerals that are insoluble in water. The choice of smelting technology we made was a pivotal factor in concentrating harmful impurities present in the copper concentrate into a single product, such as capturing arsenic with dust. ENFI, with its extensive experience in building factories in China and other countries, is well-equipped to provide technological solutions in this domain. SKS technology was selected as the primary solution to address infrastructure challenges. Now, the focus turns to determining investment costs, the level of technological automation, the source of electricity, opportunities for electricity reuse, and the utilization of heat from the smelting process as an energy source. EMC has specific proposals in this regard, awaiting resolution.
Efforts are currently in progress to construct individual smelters, including the EMC and Oyu Tolgoi. Yet, there remains uncertainty regarding whether all copper projects will be amalgamated into a single smelter. In the event of separate smelters, how open is the EMC to the possibility of accommodating other copper projects within its framework?
Indeed, two distinct projects are currently underway. The Oyu Tolgoi copper smelter project has been managed separately within the Copper Project Unit under the Ministry of Mining and Heavy Industry (MMHI). The decision by the Prime Minister of Mongolia in 2023 to establish the National Committee for Industrialization, with the Minister of Mining and Heavy Industry as its head, was a prudent move. This committee comprises three sub-committees, and it is expected to address numerous issues, particularly within the Copper Subcommittee. The volume of concentrate produced by Oyu Tolgoi is expected to increase in the future, potentially reaching 1.8-2 million tonnes. However, it's important to recognize that this quantity may not remain constant for an extended period and could decrease after a few years. There may be considerations regarding the possibility of not smelting all the concentrates within Mongolia. It becomes feasible to construct a facility with a onemillion-tonne concentrate capacity and sell one million tonnes as concentrate. The preliminary feasibility study for such a smelter with a one-million-tonne capacity has been conducted at the Project Unit, along with obtaining land and water permits. If Oyu Tolgoi decides to build a one-million-tonne concentrate smelter, and it becomes unfeasible to smelt the concentrates from other companies, there could be a need to expand the Erdenet smelter. Detailed design work can now be undertaken with this concept in mind. Of course, careful consideration is required concerning the capacities of these two projects and the duration they will operate at specific capacities. The Erdenet project remains open to further discussions and deliberations. The EMC is actively addressing significant infrastructure challenges, and the Industrial Technology Park represents a substantial state investment. It's essential to explore avenues that avoid competition with the private sector and state industries and do not result in market closures. Decisions on these matters may require additional government regulation, which can be determined by the National Industrialization Committee and other relevant authorities.
Precisely where will the location be, and what specific infrastructure challenges have been successfully addressed?
The site will be situated within a 1,200-hectare area of the Erdenet Industrial and Technology Park. The construction of the infrastructure for the copper concentrate smelter within the Industrial and Technology Park necessitates an investment of over USD 40 million or approximately MNT 140 billion, funded by EMC. All essential components, including feasibility studies, design, land permits, environmental assessments, and financing, have been meticulously addressed. We have ensured the provision of comprehensive infrastructure amenities, encompassing water supply, electricity supply, as well as road and railway networks. Currently, 55% of the railway construction work and 35% of the road construction work are in progress.
Nyamtaishir. B of MAK has expressed his disagreement with Erdenet's proposed establishment of a copper smelter in Erdenet, citing several reasons. Firstly, he argues that, in light of Mongolia's potential to produce 2.4- 3.6 million tonnes of concentrate in the future, it is essential to construct a single economically efficient smelter. Secondly, he advocates for locating the copper smelting refinery in the southern region, taking into account the potential new copper deposits and discoveries that may arise in the future. Lastly, he posits that the economic viability of the copper smelter would be achieved by melting and refining 1.2-1.5 million tonnes of concentrate. How would you address these points?
The idea of constructing a smelter in Mongolia has been part of the discussion since the inception of EMC. Up until the 1990s, initial calculations and feasibility studies were conducted, exploring the possibility of utilizing Khuvsgul Phosphorite deposits. Had there not been a democratic revolution, and Mongolia had not transitioned to a market-based society, with the social system remaining unchanged, a smelter would have likely been built in Erdenet, with Burenkhaan's phosphorite deposits being considered. The process of selecting the most advantageous location for a smelter has been carried out on multiple occasions. Even entities like the Japanese International Cooperation Agency "JICA" and the Canadian company Hatch were involved in conducting feasibility studies, under the auspices of the Mongolian Government. These studies involved a comparison of several parameters and identified Erdenet as the most feasible location among the 5 to 6 sites considered in Mongolia. Mr. Nyamtaishir's suggestion that Bor-Undur is a potential location offers an alternative perspective. Notably, Bor-Undur had also been examined by the aforementioned foreign organizations. EMC has undertaken the development and discussion of a feasibility study regarding the potential establishment of its copper concentrate smelting and processing plant in Bor-Undur. Interestingly, a few years ago, the Minister of Industry participated in a ribbon-cutting ceremony for the construction of a copper concentrate smelter in Bor-Undur during my time there. However, it's worth noting that a decision in that regard was not finalized by the Ministry, suggesting that there may have been compelling reasons for their choice. The primary reason for favoring Bor-Undur as a location hinges on the question of what to do with the sulfur dioxide generated in the process. A Swiss company, commissioned by Erdenet, conducted research into the conversion of sulfur dioxide into sulfuric acid, which would be mixed with 97% fluorine concentrate from Bor-Undur FPP to produce hydrogen fluoride. This concept gained considerable attention at the time but gradually receded from the forefront of consideration. Several factors contributed to this shift, including the high cost associated with producing 97% fluorine concentrate in Bor-Undur, the limited utility of hydrogen fluoride alone, the need for aluminum oxide (bauxite) to manufacture cryolite (which Mongolia lacks), and the challenges tied to transporting hydrogen fluoride, requiring substantial quantities of sulfuric acid, among other considerations. Additionally, establishing a factory in BorUndur would necessitate significant investments in infrastructure. Challenges include limitations in railway freight capacity, difficulties in ensuring a reliable electricity supply, and the requirement to draw underground water from sources located 50- 60 kilometers away through water pipelines. This infrastructure poses unique challenges, particularly given the age of the existing pipeline, which requires re-lining. Previously, it had been stated that EMC was addressing all infrastructure concerns at the FPP location using its resources. Currently, there are 124 copper concentrate smelters globally, with approximately 104 of these facilities producing cathode copper within the range of 100,000 to 300,000 tonnes. According to the feasibility study, the proposed copper concentrate processing plant in Erdenet is expected to have the capacity to produce 120-130 thousand tonnes of cathode copper. As I mentioned during my speech over the Mining Week it's well understood that higher capacity can lead to lower operating costs, emphasizing the significance of the feasibility study's findings.
What is the rationale behind opting for a copper concentrate processing plant with a capacity of up to 900,000 tonnes? China has numerous small factories with similar technology. Could a larger facility have been a more suitable solution?
As previously mentioned, Erdenet's concentrate production stands at around 560,000 tonnes. Several factors influence the choice of a copper concentrate processing plant with a capacity of up to 900,000 tonnes. Considerations include detailed design for potential capacity expansion, planning for expandable areas, their intended use, and the relative placement of components. While a high-capacity plant may seem economically advantageous, opting for a lowercapacity plant mitigates Mongolia's risk, particularly concerning sulfur gas processing technology, potential uncertainties in the final and by-product sales market, and the feasibility of the project's initial stages. Additionally, there's an option for capacity expansion in the design. Furthermore, when considering the possibility of melting and refining concentrates from Tsagaansuvarga and Kharmagtai mines in the planned Erdenet smelter, the decision was to design it as a lower-capacity plant, up to 900,000 tonnes. These mines, which are yet to be operational, are owned by the private sector, with the Kharmagtai deposit being more gold-dominated than copper. The focus is likely to be on gold extraction technology, and reserves will be recalculated in due course. It's understood that China's "Zijin Mining" has acquired a significant stake in this venture. Given the uncertainty about when these mines will commence operations and whether we will be smelting their copper, it makes sense, to begin with a factory that suits our current capacity and expands as needed. Depending on the investment scenario, the smelter is expected to operate independently of EMC, with reduced social and management costs, adopting a more market-driven approach.
The investment currently stands at USD 762 million. Is there a likelihood that this figure may increase?
Before the COVID-19 epidemic, the estimated investment was USD 762 million, as indicated in the feasibility study approved by MMHI. However, an update to the Feasibility Study is warranted based on the results of the elemental sulfur pilot plant. At the time, MMHI had not provided a clear stance on the issue of elemental sulfur, making it necessary to focus on product quality through production tests and clarifying the technological procedures. The pilot plant was established in collaboration with ENFI Engineering, and it's estimated that the elemental sulfur plant will account for over 20% of the total investment. The specific quantities of materials, substances, and reagents required for elemental sulfur production, the expected elemental sulfur output, and how other elements' quantities will be affected will be determined in detail. The production of elemental sulfur promises to address numerous environmental concerns. While most of the world's copper concentrate smelters currently use sulfuric acid as an alternative, recent interest in producing elemental sulfur by processing sulfur dioxide gas has emerged due to the characteristics of raw materials and plant location. This shift aligns with policies aimed at implementing this technology. The preference for sulfuric acid is mainly due to its ease of use and lower initial investment. Countries with developed chemical industries typically rely on sulfuric acid as their primary raw material, whereas our country imports it. It's utilized by factories employing solution concentration technology. It's worth noting that, with the future implementation of the uranium project, sulfuric acid consumption in Mongolia is expected to rise.
You mentioned the significance of strategic investors in copper concentrate smelters. Could you specify who these investors might be? Will they primarily consist of technology owners, copper concentrate suppliers, or buyers? Additionally, in terms of the companies supplying copper concentrate to the smelter, is there a requirement for them to hold a specific amount of shares to assure the smelter? Are foreign investors also expected to participate in this context?
I believe that relying on a "turnkey" approach for constructing a factory that's expected to operate for many years carries certain risks. To ensure the factory's continuous, stable, and reliable operation over an extended period, it's advisable to involve the construction company as a strategic partner. In this way, the factory can be built with a strong focus on quality, long-term reliability, and mutual interest in its profitable operation. Ideally, the construction party should have a vested interest in the factory's future profitability and successful production. We aim to partner with entities that possess relevant experience in constructing factories of a similar scale, have proprietary technology, and are open to investing and holding a certain share in the project. This could potentially involve significant Chinese companies with recent experience in building smelting plants, Finland's OUTOTEC, or any other partners willing to invest 10-15 percent in our plant and acquire a stake. We are open to engaging in negotiations with interested parties. It's important to note that the primary objective behind building the smelter extends beyond the production and sale of cathode copper. Our government's policy aligns with processing copper within Mongolia and generating higher-value products. The establishment of a legal framework supports this direction. By constructing our factory and producing hightech products that go beyond cathode copper, we can transport these high-value items by air rather than solely relying on rail transportation to reach a seaport. Copper plates (foils) and copper powder are currently highly regarded. EMC has a longstanding partnership with Samsung Corporation, and we have explored the potential for cooperation in the high-tech sector at the Industrial and Technology Park during the visit of Samsung's Vice President. This avenue of collaboration is being further considered. Additionally, weare in the process of preparing a feasibility study for a cable telephone plant at EMC to meet domestic needs. A Japanese company has expressed interest in cooperating on a copper plate factory, and discussions are underway regarding this opportunity. Hence, the objective is to attract companies that have experience in constructing and operating nextlevel factories, have established a foothold in the market, possess proprietary technology, and are willing to collaborate. Access to markets and establishing a presence within them can be challenging without cooperation with such well-positioned companies. Engaging in partnerships and collaborating with manufacturers of end-products and key industry players will be our gateway to selling our products effectively. As of now, no partnerships with any company in any field have been established. This aligns with the defined policy, but extensive research is underway. Determining the share of a strategic-level investor will be a subject of discussion at the policy level, including Erdenes Mongol LLC, its board of directors, and the National Industrialization Committee. It's worth noting that Erdenet's current buyer collaborations are solely focused on purchasing concentrate from Mongolia and do not support the policy of building a smelter.
The progress of the smelter has been hindered in recent years, mainly due to concerns from concentrate buyers, environmental factors, and domestic political considerations. The selection of appropriate technologies will help address the environmental challenges, and it appears that concentrate buyers may reassess their stance. However, has there been any political or internal political resolution to these issues?
Building a smelter is a complex challenge that goes beyond the scope of EMC alone. Various concerns have been raised, such as the need for phosphorite, environmental impacts, sulfuric acid management, permafrost preservation, watershed conservation, and adapting to the changing times. These concerns have raised uncertainties and reduced enthusiasm. To address these challenges, a National industrialization committee has been established, comprising ministers and industry experts, with the Minister of Mining and Heavy Industry serving as its head. The committee has formed sub-committees in three main areas, involving stakeholders from various sectors. This inclusive approach allows for a comprehensive examination of the issue and the opportunity for all parties to express their views. It is expected that, after a thorough consideration of all aspects, a unified political solution will be reached. The Copper Subcommittee is set to convene soon to finalize the matter related to the smelter's location.
What does the future hold for EMC if a smelter is not built? If the ore received has a grade of 0.3% and the copper content in the concentrate drops below 22%, does this mean that the company may not meet contractual obligations, potentially jeopardizing its financial stability and business continuity?
It may be premature to make a definitive statement at this stage, but the future outlook suggests challenging times. There are several factors contributing to this concern, 1. The quantity of concentrate available for sale is gradually decreasing, leading to reduced revenue. 2. As the quality and copper content of the concentrate decline, the number of potential buyers may decrease, eventually resulting in a lack of interested purchasers. 3. New, high-grade deposits, similar to Kamoa-Kakula in Africa, may emerge, attracting attention from the market. To ensure the long-term stability of EMC operations, the construction of downstream product facilities following the smelter becomes paramount. EMC is poised to strongly advocate for this project because the intersection of utility and necessity converges at one crucial point: the establishment of the smelter. Comprehensive planning for the company's assets is also underway to address these challenges.
As a former minister in the sector and taking a broader perspective, would you have chosen to name the smelter location exclusively after Erdenet, or would you have considered a more inclusive name that reflects the collaborative nature of the project and serves various stakeholders in the industry?
Erdenet's stance remains unchanged. I come from a family of miners; I'm a mining engineer myself. My father was also deeply involved in mining. I spent a decade in academic pursuits and over 20 years working in the mining sector, particularly in rural areas. My ministerial role was relatively short, spanning only 2 years and 2 months. I believe that politicians often make decisions guided by their "hearts," whereas engineers tend to rely more on their "heads," which means numbers and calculations. Numbers are devoid of emotions; they represent rational thinking. This is why, when Prime Minister Oyun-Erdene. L visited Erdenet in May 2021, he entrusted the special permit for the Industrial Technology Park to the director of EMC. This decision was made during my tenure as a minister. The construction of a copper concentrate processing plant is considered a vital task for the industry. Erdenet's day-to-day production processes are highly efficient. Beyond the copper concentrate smelter, there are various initiatives underway that are worth noting. For instance, there are efforts to ensure transparency in procurement and tender processes, which is crucial for a thriving mining sector. Much planning and execution have gone into achieving fair, transparent, and open procurement and tendering in the mining industry. In this regard, we are actively studying technological opportunities and best practices from foreign countries. We are also collaborating with leading IT companies, the State Procurement Department, and the Ministry of Electronic Development and Communications. The results of these efforts will be released soon. During my ministerial tenure, I worked on making the process of issuing exploration licenses open, electronic, and transparent. The perception used to be that only wrestlers and IT experts secured these licenses. However, now, when you visit www.tender. gov.mn, you'll find a section dedicated to "Minerals." This step is intended to demystify the process of obtaining licenses and address many of the negative perceptions that have tarnished our industry's reputation. We're steadily moving towards creating a more level playing field.
What is the current estimate for the ore reserve at Erdenet, and are there varying reports regarding its potential duration, such as 40-year or 70-year reserves?
Erdenet's resources are projected to last for 60- 70 years, but based on our initial assessments, the efficiently usable reserves are estimated to span around 45 years. These reserves amount to approximately 2.9 billion tonnes of ore. Nonetheless, a comprehensive feasibility study is currently in progress to assess the utilization of these updated resources. A tender was issued, and an experienced Australian company partnered with a Mongolian firm to secure the project. We've engaged with them to outline our specific requirements, and the feasibility study will yield more precise figures. There is even the possibility of some resources being extracted through underground mining. Erdenet is a state-owned industry with significant social responsibilities, contributing over 10% of the state budget. Given its paramount importance, the longevity of the mine is a critical consideration. Maximizing the utilization of lower-grade resources will extend its lifespan. Consequently, there are numerous future initiatives and projects to be implemented. Recent years have witnessed robust demand for copper, and foreign market conditions have been relatively favorable. In 2022, EMC made a historic contribution of MNT 1.8 trillion to the state budget, with total sales reaching MNT 3.7 trillion. Based on the expected performance for this year, the contribution to the state budget is projected to reach MNT 2.0 trillion. However, copper prices have faced some challenges in the fourth quarter. During the LME Week, leading experts in the copper industry anticipate a steady rise in copper prices through the first half of 2025, with a bit of uncertainty in 2024.
What is the composition of the waste materials produced by EMC?
There are two types of stockpiles in Erdenet. It is incorrect to refer to them as piles; "stockyard" is the accurate term. Oxidized ore stockpiles comprise ores that are unsuitable for processing due to oxidation, even if they have a high copper content. However, the quality of low-grade ore stockpiles has varied over time. Initially, ore with a copper content of 0.5-0.6% might have been discarded. During that period, the average ore grade from the mine was around 0.7- 0.8%, so anything falling below this threshold was placed in the low-grade ore stockpile. Currently, with an anticipated drop in the average ore grade from the mine to 0.38% by 2024, ore with 0.4% content will be sent to the concentration plant. The stockpiles used by Achit-Ikht are for low-grade ore, not oxidized ore. It's also possible that some of the low-grade ore stockpiles were formed during periods when the marginal ore grade was higher, so some sections may contain higher grades compared to what is currently being mined.
How is the actual operating cost increasing as a result of the declining ore grade in the mining industry? And, in a general sense, what measures are taken to manage these rising costs and maintain financial balance?
Typically, operating costs stand at approximately USD 6,700 per tonne, inclusive of social costs, which, while significant, make up only 6-7 percent of the total expenses. The C1 production cost is below USD 6,000 per tonne. The primary driver behind the cost escalation is the rising prices of electricity and materials. A cost of USD 6,700 per tonne remains reasonable. During the recent LME Week, many factories and mines reported worsening geological conditions. Given that large-scale mining in our country commenced relatively late, we have fared comparatively well. Several copper deposits have been developed, and their operating costs are at USD 7,500 per tonne. Some analysts speculate that the price of copper could drop to USD 7,500 next year, which might lead most major producers to halt production. However, these predictions may not materialize as expected. Competitively, the USD 6,700 per tonne cost remains favorable for the precious metals industry. In next year's business plan for EMC, a proposal has been submitted to calculate the copper price at USD 8,650 to Erdenes Mongol LLC, while there is a budgeted figure of USD 9,000 in the state budget.
What proportion of the overall expenses is represented by labor costs? How are the employees at Erdenet managing wage hikes and addressing other requests?
Wages for employees make up less than 20 percent of the total expenditure, which is reasonable considering the wealth generated. In the past, during the joint venture phase governed by international agreements, there were instances of substantial wage increases, sometimes up to 70 percent in certain years. After the transition to a State-Owned Enterprise (SOE), a Collective Bargaining Agreement was established, providing for a 10 percent annual salary increase. Erdenet's wages are relatively high compared to other state-owned mines, estimated to be 1.5 times above the industry average. However, salaries in privately owned foreign-invested companies are higher. Due to changes in the exchange rate, salaries have not increased when converted to USD since 2016. As a result, a 15% salary increase proposal was submitted in June to the Government Secretariat and later approved by the management of Erdenes Mongol LLC in August. Nevertheless, the Trade Union demanded a 50% increase, leading to negotiations and, eventually, a strike. The strike was halted after 8 hours, with the factory continuing to operate. The General Director engaged with the striking workers and explained the financial constraints. It was mutually agreed that a 50% increase was not feasible, and the factory should remain operational while continuing negotiations. The negotiations are ongoing, with both parties presenting their calculations and justifications to each other. Another topic discussed during negotiations was the provision that retiring factory workers could secure employment for their children at EMC. Given the challenging mining conditions and rising costs, the factory intends to maintain productivity by hiring skilled professionals for years to come. Simultaneously, Erdenet is a workplace for all 3.5 million Mongolians, not just those with familial connections to current employees. The concept is to ensure that individuals from various regions, including the East, Uvs, and Ulaanbaatar, have opportunities at the factory. This perspective is shared by the miners, who have a deep affection for the factory and recognize the importance of equal opportunities for all.
Is there a plan to implement a conveyor system within the open-pit mine?
During the COVID-19 period, several projects faced interruptions due to price hikes, with some companies raising their costs. These price increases were sanctioned by the Construction Development Center and the State Property Committee, making it relatively straightforward to allocate them within the approved budget. However, as someone with a background in production and construction, certain figures and calculations appeared impractical and unacceptable. Consequently, an international audit was initiated, resulting in a substantial reduction of over 60% in the previously approved price hikes. While some companies expressed discontent and a few even protested, one company has chosen to take the matter to court. Nevertheless, most companies have accepted the revised terms, signed contracts, and resumed their work. Among these companies is one that is actively engaged in implementing a conveyor system project, scheduled for completion in July 2024. This project not only aids in cost reduction but also offers environmental and safety benefits, especially with the rising price of diesel fuel. Additionally, due to declining ore grades from the mine, there's a need to expand the final contour of the mine, for which the conveyor system will be employed. There are also plans to utilize it for ore transport to the mill.
What areas is EMC currently focusing on to determine its future direction, in addition to the copper smelter project?
the city itself can be considered a mine, requiring a constant increase in resources. EMC holds six special exploration licenses within the strategic deposit boundaries, crucial for the longevity of EMC. History has shown that towns and cities often face difficulties when mines close, not just in our country but globally. Hence, it is vital to manage the closure of EMC meticulously. In addition to expanding reserves regularly, we need to undertake efforts related to the mine's future and the next stage of production. Firstly, we are consistently investing in expanding our reserves. Secondly, we are diligently working to maximize the utilization of existing resources, implementing costcutting strategies and adopting energy-efficient and labor-saving technological innovations that allow the plant to operate profitably even as ore quality declines. Extensive expansions and renovations are underway, although we still contend with outdated equipment from the Soviet era. Thirdly, we are devoting significant efforts to establishing a copper concentrate smelting plant, which would not only maintain the mine's current profitability but also generate more revenue by producing hightech, high-value, and profitable products using existing resources. Fourth, a significant focus is placed on ESG issues. EMC, as the first state-owned enterprise to issue an ESG report, is committed to incorporating renewable energy sources for some of its units and sections. We understand the importance of aligning our activities with global carbon policies, fulfilling our commitments under the "Billion Trees" national program, calculating our factories' CO2 emissions, and taking gradual steps to reduce them. This aligns with our long-term vision to transition heavy-duty dump trucks in open-pit mines to electric engines. We firmly believe that embracing transparency and reporting will ultimately contribute to avoiding potential carbon taxes on our products. Notably, certain minerals already face carbon taxes when crossing the borders of the European Union. We anticipate close alignment between the "Billion Trees" national program and our industry's carbon policy. In the initial phase, we are calculating the feasibility of supplying remote facilities such as the "Selenge Recreation and Tourism Complex," the "Green Development Center," and the "Tree Breeding Complex" with renewable energy. Additionally, in 2022, EMC SOE established a "Forest Genetic Resource Center" with a diverse seed bank. In 2023, we will launch the "Soil Biotechnology Center," which is set to begin operations this October. Based on soil and seed resources, we are creating a tree-breeding complex in Khyalganat. This facility will enable us to propagate trees rapidly and nurture their growth. Traditional greenhouses will cover 90 hectares, with an additional 10 hectares for automated greenhouses. The Feasibility Study for the automated greenhouse complex was developed in collaboration with the Institute of Biology of the Mongolian Academy of Sciences and successfully defended at the Ministry of Environment and Tourism in August. A tender for the construction of automated greenhouses capable of propagating 12 million trees annually will be announced shortly. It is worth noting that in 2013, a joint assessment by the Ministry of Environment and the World Bank estimated EMC's CO2 emissions at 1 million tonnes, a figure that has since risen to nearly 2 million tonnes. This increase is due to factors such as the expansion of thermal power plant capacity by 48 MW since 2013 and the addition of more BelAZ trucks. Furthermore, the construction of a smelter is expected to release additional CO2 emissions. It's essential to understand that tree planting plays a critical role in absorbing CO2 emissions, effectively reabsorbing an equivalent amount while releasing oxygen.
Thank you for the informative conversation.
Mining Insight Magazine, №10 (023)